Glass bottles are a ubiquitous packaging choice, utilized for storing and showcasing a diverse range of items, from food and beverages to cosmetics and perfume. Crafted from the versatile material of glass, these bottles possess a myriad of distinctive characteristics and advantages.
The process of crafting glass bottles commences with the meticulous selection of glass raw materials. Commonly employed materials include silica, sodium carbonate, and limestone, among others. Through the amalgamation and subsequent heating of these ingredients, a molten glass substance is formed.
Next, the molten glass is injected into meticulously designed molds. These molds can be customized to accommodate the desired shape and dimensions of the bottle. Once the glass is within the confines of the mold, it gradually cools and solidifies, taking on the foundational shape of the bottle.
Post-cooling, the glass bottle undergoes a series of processing steps to achieve its final form. These steps encompass cutting, polishing, and buffing, all aimed at ensuring a smooth and refined bottle neck, devoid of any sharp edges.
Lastly, the glass bottle undergoes thorough cleansing and quality inspections. The washing process guarantees the internal and external cleanliness and hygiene of the bottle. Simultaneously, quality checks are conducted to ensure the absence of any flaws or defects, thereby meeting the exacting demands and standards set by customers.
In summation, the production process of glass bottles entails multiple stages, including material selection, melting, mold injection, cooling, processing, cleansing, and quality inspections. With meticulous craftsmanship and stringent controls at each juncture, these steps ensure the attainment of a final product imbued with superior quality and functionality.
If you want to make high quality glass container, plz contact valiant group.
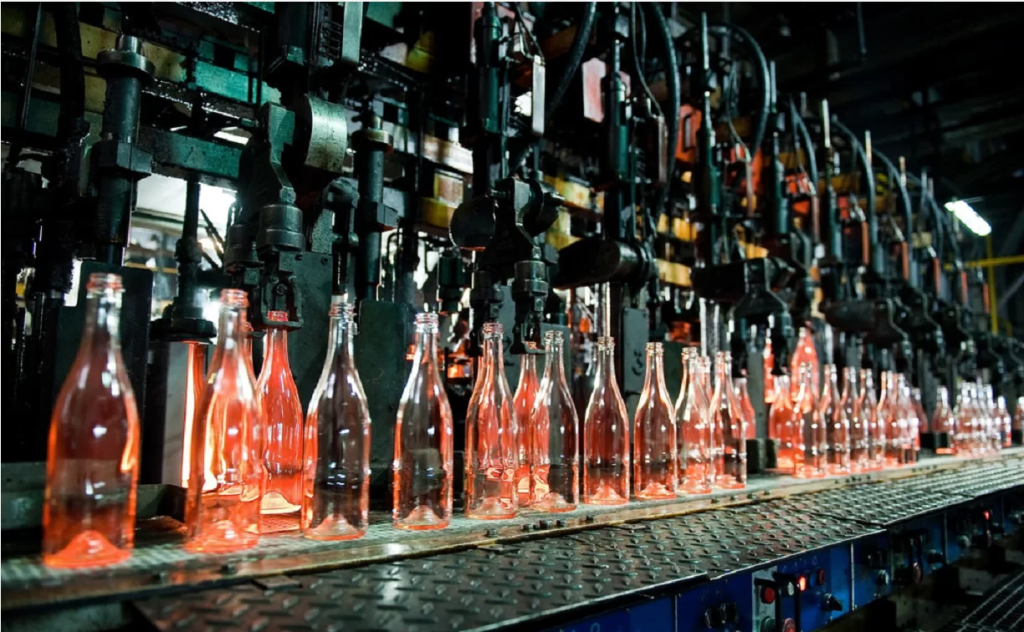