Molded glass is fed by gravity into a molding machine, where pressure forms the mouth and basic shape of the bottle. Once the neck is complete and the general glass bottle shape has been achieved, the form is called the template.
Creating terrariums can be done with one of two different processes – blow and blow, or press and blow processes. Each process is selected according to the type of glass bottle being made. All glass bottles start with raw materials. Silica (sand), soda ash, limestone, and broken glass (recycled glass that can be used in furnaces) are combined into a specific mixture based on the desired characteristics of the bottle. The mixture is then melted at high temperatures in a furnace until it becomes a molten material, ready for molding. This mixture will produce a type of glass called sodium-calcium glass, which is the most popular food and beverage glass.
Once the bottle is fully formed, regardless of the process used, it is removed from the mold and transferred to the annealing furnace. The annealing furnace reheats the glass bottles to a temperature of about 1,050 degrees Fahrenheit, then gradually cools them down to about 390 degrees. This process allows the glass to cool at an even rate — eliminating internal stresses in the glass that can cause cracking or breakage. The bottles are then carefully examined to ensure they meet quality control guidelines. Any defective bottles, including bubbles, cracks or malformed areas, are removed from the production line and used as broken glass. All remaining bottles are sorted according to size and type. Bottles are then packed on pallets and ready for transport.
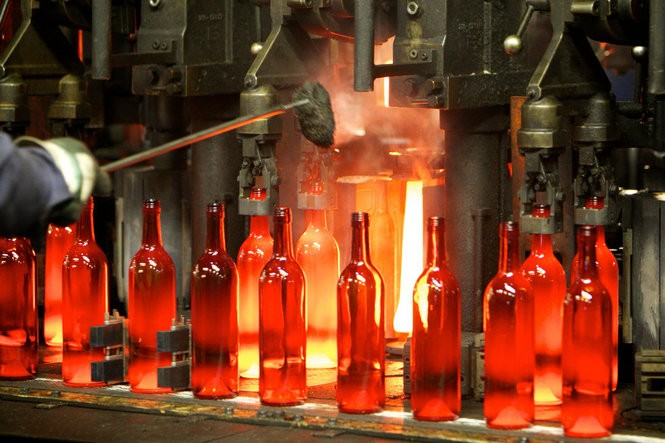