In order to keep the mold temperature within the range specified by the process, the heat preservation and cooling of the mold are extremely important measures. The glass frit formed in a viscous state must be fully cooled in the mold to maintain its shape after leaving the molding machine. During the molding process, a large amount of heat is dissipated from the mold wall due to cooling. The cooling method is as follows.
glass bottle production plant
Natural cooling in the atmosphere: due to the limited heat transfer capacity of the metal mold itself, natural cooling is only suitable for low molding speeds. Generally, this method is mostly used in manual work, especially when blowing hollow glass manually.
Periodically immerse the mold in water for artificial cooling: when cooling the wood or graphite mold in this way, the water vapor layer formed between the mold and the glass acts as an isolation and lubrication layer. This method is suitable for artificial blowing and automatic forming of thin-walled seamless glass.
Cool the mold with one or several streams of compressed air (direct blowing or oblique blowing to the mold wall): this method is the most widely used in hollow glass molding.
Depending on the cooling position, the outer wall can be continuously cooled or the inner wall of the mold that is in contact with the glass can be directly cooled periodically, or both methods can be used at the same time.
In addition to air, there are also proposals for cooling with other coolants, such as evaporative cooling and recirculation cooling using sodium as a coolant, as well as water cooling.
The inlet temperature, flow rate and water quality requirements of the cooling water are different according to the product production rate, mold material, shape and thickness of each part. Taking the picture tube glass bulb mold as an example: the cooling of the glass screen convex mold Water flow 20L/min water pressure 0.3MP.
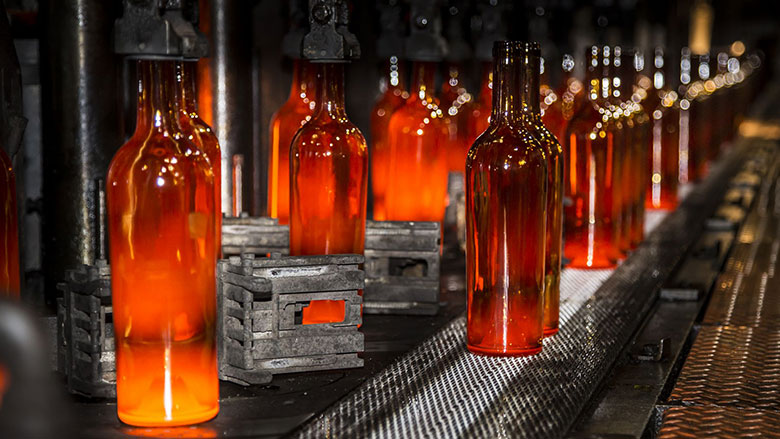