the process of making glass bottles is a combination of both the machine and the human workforce. here are the general steps involved in glass bottle manufacturing:
batch mixing: the raw materials, which typically include silica sand, soda ash, limestone, and other additives, are mixed together with water to form a batch mixture. the resulting mixture is then melted in a furnace at high temperatures of about 1,500 degrees Celsius.
bottle forming: the molten glass is shaped into a hollow bottle by using a machine called an is machine (individual section), which consists of multiple sections that work together to form the bottle. the machine uses compressed air to blow the molten glass within the cavity of a mold.
cooling and annealing: after shaping, the formed bottles are immediately cooled in a cooling chamber to reduce their temperature quickly. the cooling must be done appropriately to avoid any deformation or cracking of the bottles. once they reach room temperature, the bottles go through a process called annealing which helps to relieve any residual stresses and strengthens the glass.
quality control: glass bottles undergo several quality checks such as dimensional accuracy, wall thicknesses, weight, appearance, and mechanical strength to ensure they meet industry standards and customer requirements.
packaging: the final step involves the packaging of the glass bottles and shipping them to customers. the packaging must be done carefully to avoid damages.
in summary, these are the general steps involved in making glass bottles. while the basic process is the same, the details may vary slightly depending on the specific type of bottle being made and the desired quality.
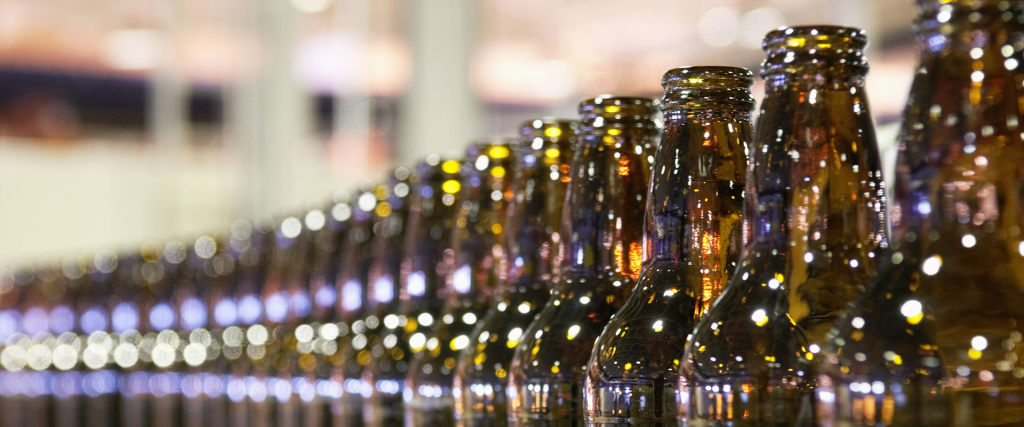